Table of Contents
- Introduction to ScopioneCarbon
- What is Carbon Fiber?
- How is Carbon Fiber Made?
- What is ‘Grade A’ Carbon?
- What is the Difference Between Wet and Dry (Pre-preg) Carbon Fiber?
- What is Dry Carbon Fiber?
- What is Wet Carbon Fiber?
- What is Pre-preg Carbon Fiber?
- What is a Weave?
- What is the Difference Between 1×1 and 2×2 Weaves?
- What are Epoxy, Vinylester, and Polyester Resins?
- What are Surface Treatments and Finishes?
- What are Advantages of Carbon Fiber in Automotive Applications?
- Other Terms Explained
- Frequently Asked Questions (FAQs)
- Care and Maintenance of Carbon Fiber Parts
- Summary
Introduction to ScopioneCarbon
Scopione Carbon Fiber Parts are meticulously crafted using only the most reliable and proven formulas of epoxy resins and pre-preg Toray dry carbon sheets. This results in some of the strongest and most durable products available on the market. Our commitment to excellence is further demonstrated by the premium UV-resistant clear coat applied to each part, ensuring long-lasting protection against fading and maintaining a brilliant shine.
We take immense pride in offering only the highest-quality carbon fiber aftermarket automotive and motorcycle parts available today. Each product we carry is designed to meet the exacting standards of performance enthusiasts and professionals alike.
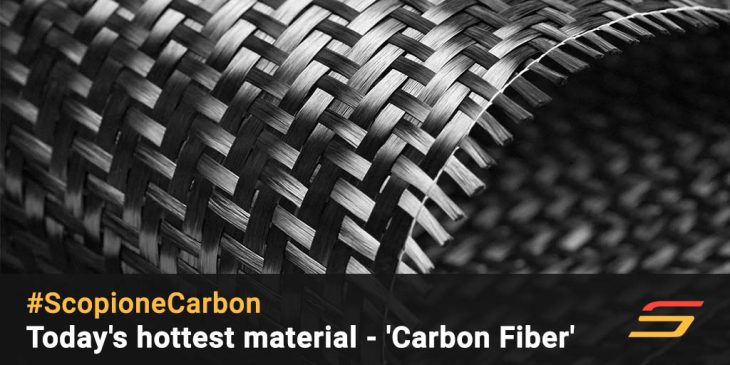
At Scopione, we understand that carbon fiber technology, while increasingly popular, is still relatively new and can be confusing to some. To support our customers in making informed decisions, we have created a dedicated section below that explains key terminology related to carbon fiber. This glossary covers everything from the material’s composition to its unique performance characteristics. Additionally, our knowledgeable team is always available to provide personalized assistance and answer any questions about the carbon fiber parts we offer.
The growing availability and affordability of carbon fiber are a direct result of innovations by manufacturers who have expanded production capacity, optimized costs, and developed new applications for this versatile material. In the automotive industry, carbon fiber is not only celebrated for its superior strength-to-weight ratio but also for its ability to enhance both performance and aesthetics. From increasing speed and agility to elevating a vehicle’s visual appeal, carbon fiber parts have revolutionized the way enthusiasts and manufacturers approach automotive customization.
Despite its relatively recent adoption in the automotive and motorcycle industries, the use of carbon fiber has grown exponentially over the years due to advanced manufacturing processes. These technological advancements have made it possible to produce parts that are significantly stronger and more impact-resistant than steel while being much lighter in weight. As a result, carbon fiber components have become indispensable in applications where performance, durability, and weight reduction are critical.
At Scopione, we are committed to staying at the forefront of these developments to bring our customers the very best in carbon fiber technology. By educating our customers about the material’s benefits and providing top-tier products, we aim to foster a community that values innovation, quality, and performance.
Whether you’re looking to upgrade your vehicle’s performance, enhance its appearance, or both, Scopione is your trusted source for premium carbon fiber parts. Explore our collection and experience the unmatched quality and craftsmanship that set our products apart.
What is Carbon Fiber?

Over 30 years ago, carbon fiber was considered a cutting-edge, space-age material that was prohibitively expensive and reserved for aerospace applications. Today, it has become a versatile and sought-after material, widely used in industries such as wind energy, automotive manufacturing, sporting goods, and more. Carbon fiber is renowned for being incredibly strong and lightweight, making it an ideal replacement for traditional materials like steel and plastic in high-end applications—especially in performance-driven sectors like motorsports and luxury sports cars.
At its core, carbon fiber is made of carbon—the most abundant element on Earth. Through an intricate process, the carbon is treated, spun into ultra-thin strands, and woven into fabrics. These strands are then bonded together using high-strength resins, cured under specific conditions to enhance durability, and finally cut and shaped into components. The result is a material that excels in strength-to-weight ratio, making it highly advantageous for engineering precision parts.
How is Carbon Fiber Made?
Carbon fibers are derived from base materials such as acrylic fibers (similar to those used in textiles like clothing and blankets) or from pitch, which is obtained from coal tar or petroleum byproducts. The production process involves bundling thousands of carbon fibers into threads, which are then woven into a cloth-like fabric. When this fabric is combined with resin-based epoxies, it forms an extremely rigid and durable composite material.
In terms of strength, carbon fiber is approximately ten times stronger than steel when measured by weight and significantly more resistant to deformation. For parts of comparable size, carbon fiber components can be twice as strong as steel while weighing only a quarter as much. This substantial reduction in weight can enhance a vehicle’s speed, performance, and sometimes even its safety by improving overall handling and reducing the strain on mechanical systems.
What is ‘Grade A’ Carbon?
Although there is no universal or official grading system for carbon fiber, the term “Grade A” is often used by manufacturers to indicate superior quality. However, this designation is typically a marketing term rather than an industry-standard certification. It is meant to reassure consumers that the product is made using premium materials and exceptional craftsmanship.
At Scopione, we primarily use carbon fiber sourced from Toray Industries Inc., one of the world’s leading suppliers of advanced composite materials. Toray has an outstanding reputation for producing top-quality carbon fiber, which is used by many of the world’s foremost automakers. By using such high-quality carbon fiber, we ensure that our products offer the durability, strength, and precision that customers expect from premium components.
Learn in-depth about Why Is Carbon Fiber So Expensive? Is It Worth the Cost? here:
- Why Does Carbon Fiber Cost So Much?
- Is Carbon Fiber Worth the Cost?
- When Is Carbon Fiber NOT Worth It?
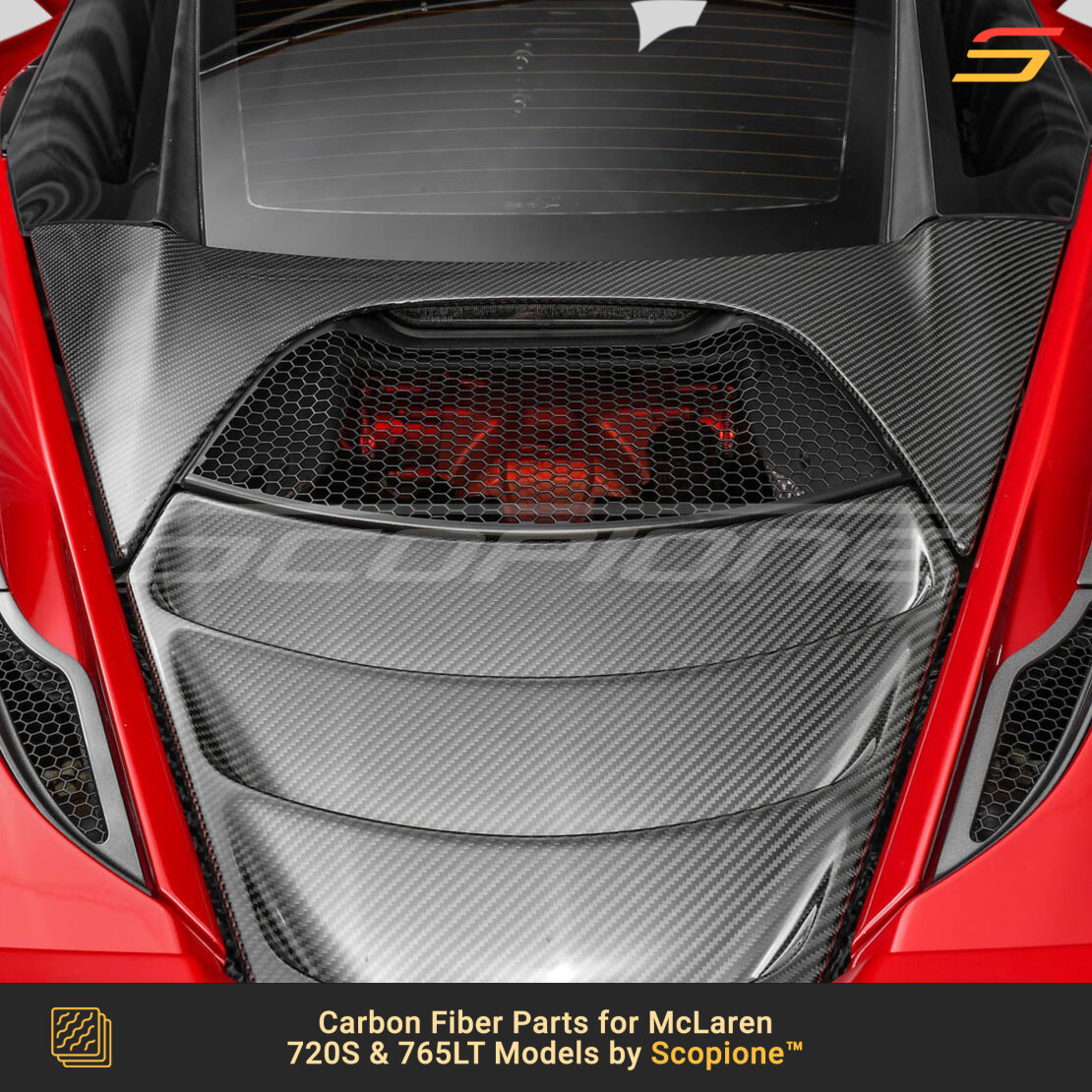
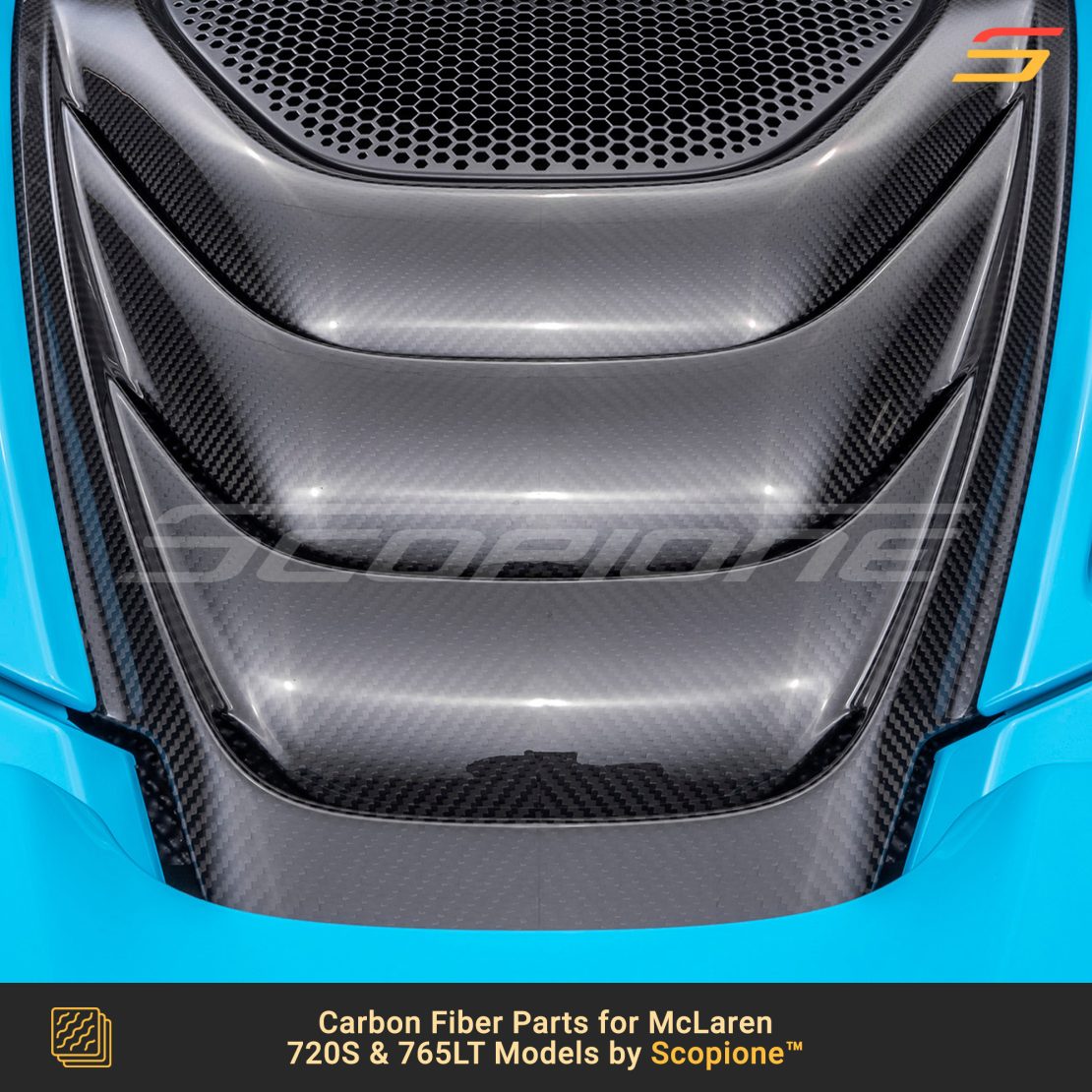
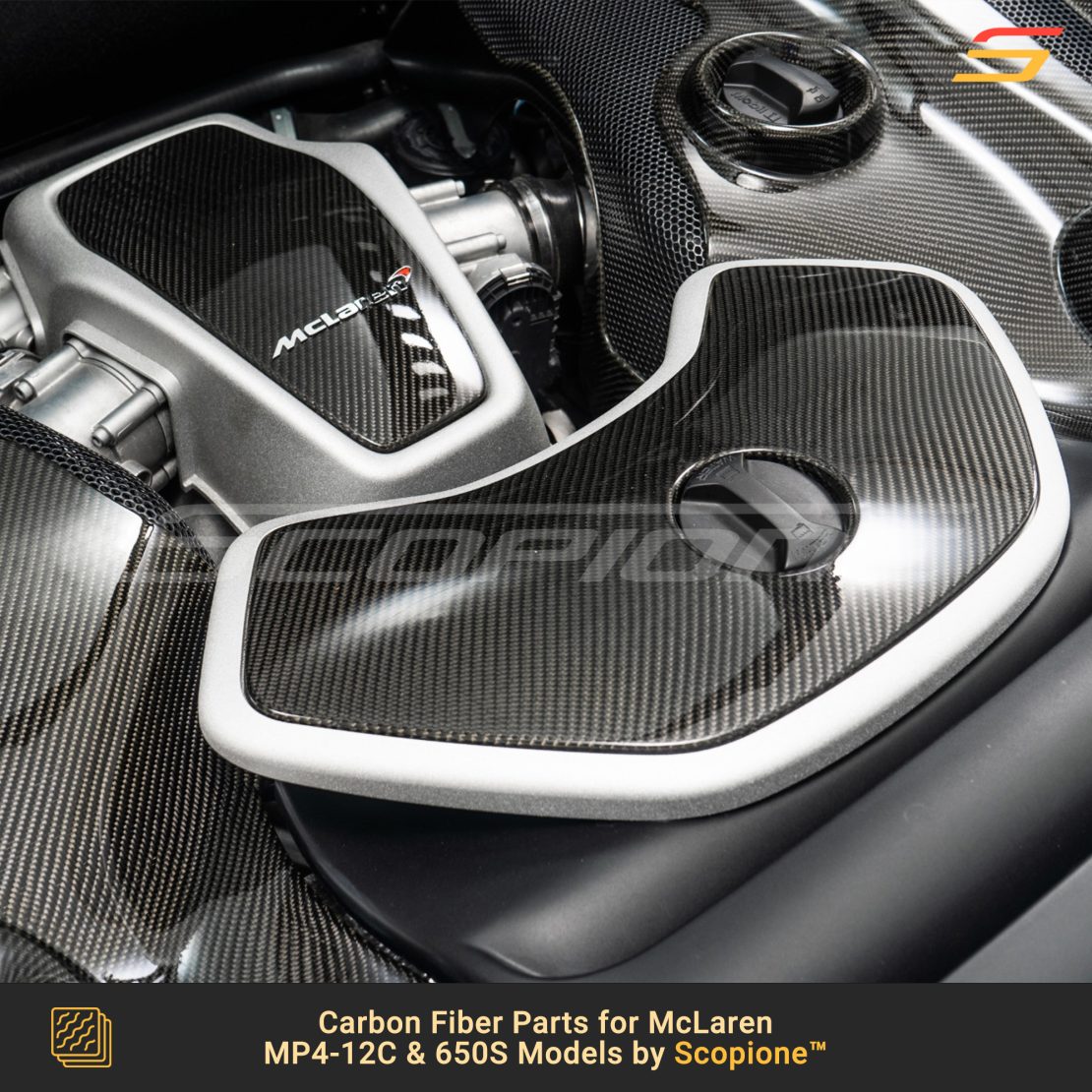
What is the Difference Between Wet and Dry (Pre-preg) Carbon Fiber?
Among the many terms associated with carbon fiber, “dry” and “wet” carbon fiber are two of the most commonly misunderstood. These terms refer to the production methods used to manufacture carbon fiber products. Each approach results in significant differences in weight, strength, and overall quality. Dry carbon fiber is made using pre-preg (pre-impregnated) resin fibers already integrated into the carbon material. In contrast, wet carbon fiber involves coating the carbon cloth with resin by hand before curing. Understanding the distinctions between these two types is essential for making an informed decision that suits your specific needs.
What is Dry Carbon Fiber?
Dry carbon fiber is formed using pre-preg carbon fiber materials, where the carbon fibers have been pre-impregnated with resin. This material is placed into a mold and then sealed in a vacuum chamber to undergo the curing process. This method minimizes waste and produces a lighter and more consistent carbon fiber product compared to the wet process. The vacuum process helps to eliminate pinholes and air pockets, resulting in a smoother, stronger, and more uniform finish. Dry carbon fiber products are regarded as the highest quality available, but this comes at a higher cost—often three to four times that of wet carbon fiber.
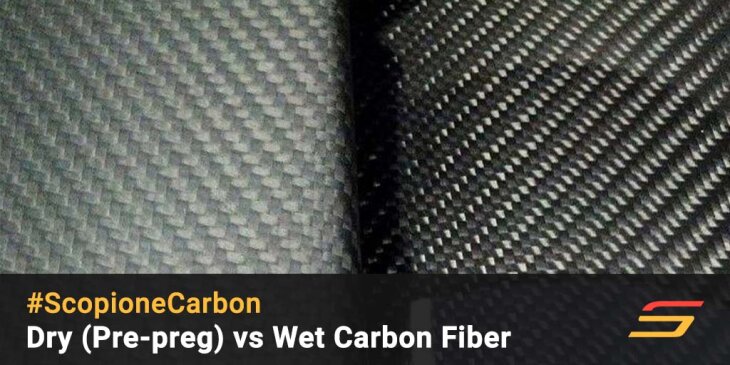
Advantages of Dry Carbon Fiber:
- Significantly lighter (up to 60% lighter than wet carbon fiber)
- Increased strength and durability
- Superior manufacturing process with minimal imperfections
- Enhanced cosmetic appearance with a sleek, dry finish
Disadvantages of Dry Carbon Fiber:
- Much more expensive to produce (three to four times more costly than wet carbon fiber)
- Requires maintenance to prevent fading unless properly coated with a UV-protective clear coat
What is Wet Carbon Fiber?
Wet carbon fiber is produced using a different, more cost-effective manufacturing process. In this method, dry carbon fiber cloth is manually laid into a mold. A resin mixture, typically a blend of two parts resin to one part carbon, is then applied over the cloth. The mold is sealed in a vacuum bag and heated to cure the resin. While this process allows for lower production costs, it also introduces a higher likelihood of air bubbles and inconsistencies, such as wavy fiber patterns. As a result, wet carbon fiber products are heavier and less durable than their dry counterparts.
Advantages of Wet Carbon Fiber:
- Lower production cost makes it more affordable for consumers
- Shiny, “wet-look” finish can be visually appealing
Disadvantages of Wet Carbon Fiber:
- Heavier and weaker compared to dry carbon fiber
- Prone to fading over time unless properly maintained
- Higher risk of imperfections, such as air pockets and uneven weaves
What is Pre-preg Carbon Fiber?
The term “pre-preg” refers to carbon fiber material that has been pre-impregnated with resin. Pre-preg carbon fiber comes in varying resin content levels, typically measured in grams per square meter (GSM). The amount of resin does not necessarily indicate the quality of the carbon fiber itself, but it does influence the material’s flexibility and curing properties.
To create a pre-preg carbon fiber component, layers of the material are placed into a mold. The mold is then covered with a breathable plastic sheet attached to a vacuum system, which removes excess air. The entire assembly is placed in an autoclave oven for curing. During this process, the mold is subjected to temperatures ranging from 350°F to 800°F and pressures of 80 to 100 psi. This high-pressure environment eliminates air pockets and non-carbon impurities, ensuring the final product is strong and lightweight. Once the curing cycle is complete, the product is allowed to cool, solidifying into a durable carbon fiber part.
The autoclave curing process is essential for creating high-performance dry carbon fiber components, making them stronger, lighter, and more resilient than those produced by the wet method.
Key Differences at a Glance:
Feature | Dry (Pre-preg) Carbon Fiber | Wet Carbon Fiber |
---|---|---|
Weight | Significantly lighter | Heavier |
Strength | Stronger and more durable | Weaker due to air pockets |
Cost | Much more expensive | More affordable |
Manufacturing | Uses pre-impregnated resin | Resin applied by hand |
Appearance | Matte or dry finish | Shiny, glossy finish |
Consistency | Minimal imperfections | Prone to inconsistencies |
Understanding the differences between dry (pre-preg) and wet carbon fiber can help you make the best choice based on your needs and budget. If performance, strength, and weight reduction are your priorities, dry carbon fiber is the superior option despite its higher cost. However, if budget constraints are a concern and you are looking for a more aesthetically glossy finish, wet carbon fiber may be a suitable alternative. Proper maintenance, such as applying a clear coat to prevent UV damage, can extend the lifespan of both types. By evaluating the pros and cons of each type, you can choose the right carbon fiber product for your application.
What is a Weave?
The term “weave” refers to the pattern formed when carbon fiber strands, known as tows, are woven into a fabric. There are many types of carbon fiber materials available, and they are typically identified by their weave pattern and tow size. Understanding the full meaning of “weave” is essential for properly evaluating and selecting carbon fiber parts for specific applications.
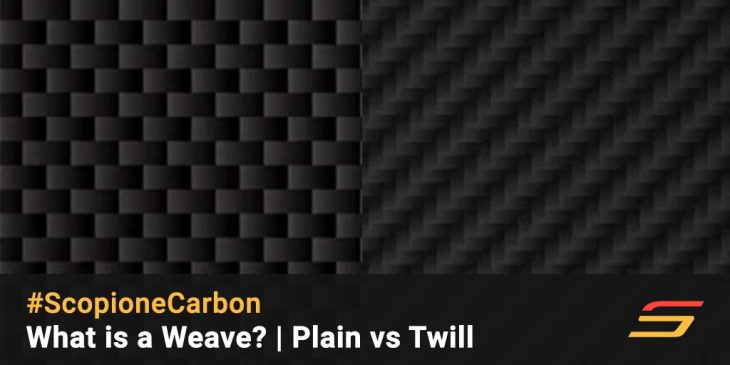
Plain Weave
A plain weave carbon fiber sheet has a symmetrical, checkerboard-style appearance. In this weave, the tows are woven in an over-under pattern, creating a balanced, uniform structure. The short distance between the interlaces provides the plain weave with a high level of stability—the ability of the fabric to maintain its weave angle and fiber orientation. This inherent stability makes plain weave carbon fiber ideal for flat sheets, tubes, and simple 2D curves.
However, the same stability limits its ability to conform to complex, curved surfaces. The rigid structure of the weave reduces its pliability, making it less suited for layups involving intricate contours. Additionally, the frequent interlacing creates sharp crimps (the angles the fibers form at each interlace point). These crimps can introduce stress concentrations, potentially weakening the part over time, especially in high-stress applications.
Twill Weave
Twill weave carbon fiber is more pliable than plain weave and can conform to complex contours while maintaining good fabric stability. This weave is popular in both structural and cosmetic applications due to its balance of formability and durability. A key feature of the twill weave is its distinctive diagonal pattern, known as the “twill line.” This pattern is created by the tows passing over and under multiple other tows in a staggered sequence.
In a 2×2 twill weave, for example, each tow passes over two tows and then under two tows. Similarly, a 4×4 twill weave follows the same principle, passing over and under four tows. The longer distances between interlaces result in fewer crimps, which reduces the risk of stress concentrations and enhances the material’s strength. This characteristic also contributes to the weave’s ability to withstand wear and minimize weak points over time.
Due to its visually appealing texture and versatility, the 2×2 twill weave is one of the most recognizable patterns in the automotive and aerospace industries. It is often used in high-end car components, accessories, and decorative carbon fiber elements.
Choosing the Right Weave
When selecting a carbon fiber weave, it is important to consider the specific requirements of the project. Plain weave offers superior stability for flat and simple shapes but may be prone to stress points due to crimping. On the other hand, twill weave provides a combination of flexibility and strength, making it a better choice for parts with complex contours or for those requiring an attractive surface finish.
By understanding the unique properties of each weave, you can make more informed decisions and optimize the performance, durability, and aesthetic appeal of your carbon fiber components.
What is the Difference Between 1×1 and 2×2 Weaves?
The difference between 1×1 and 2×2 weaves lies in the pattern of the weave itself. 1×1 weaves resemble a square or checkerboard pattern, while 2×2 weaves have a distinct diagonal appearance. With carbon fiber becoming increasingly popular, many people have questions about the different carbon fiber weaves and whether any particular weave is superior for specific applications.
1×1 Weave
The 1×1 weave carbon fiber is woven in a symmetrical, tightly-knit pattern, which gives it excellent strength and a clean, uniform look. This type of weave is commonly used in both OEM (Original Equipment Manufacturer) and aftermarket automotive parts. It is easily recognizable due to its checkerboard-like pattern.
One of the primary advantages of the 1×1 weave is its stability. The tight weave makes the fabric less prone to distortion during handling, ensuring a consistent and professional appearance. However, this tightness comes at the cost of flexibility. The 1×1 weave is less pliable, making it challenging to drape over complex molds or contours. This limitation can make it unsuitable for certain intricate shapes.
An example of the 1×1 weave’s use is in the carbon fiber roofs of high-performance cars such as the BMW M3. These applications benefit from the strength and appearance of the 1×1 weave, where fewer complex curves are involved.
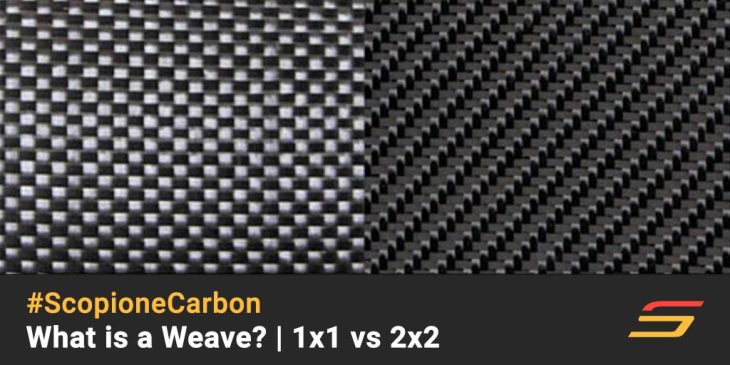
2×2 Weave
The 2×2 weave is the most common weave in the automotive industry, especially for aftermarket parts like carbon fiber hoods, splitters, and rear diffusers. It features a diagonal pattern, making it visually distinct from the checkerboard look of the 1×1 weave.
One key advantage of the 2×2 weave is its flexibility. The diagonal pattern allows the fabric to more easily conform to complex shapes and angles, making it ideal for parts with intricate designs, such as rear diffusers with integrated fins and sharp corners. This adaptability makes it the preferred choice for parts that require a high degree of draping over molds.
Comparing 1×1 and 2×2 Weaves
Both 1×1 and 2×2 weaves are strong and lightweight, making them excellent choices for automotive use. However, each weave has its own strengths and limitations:
- 1×1 Weave:
- Strengths: High stability, resistance to distortion, and a refined checkerboard aesthetic.
- Weaknesses: Less flexible and harder to mold into complex shapes.
- Cost: Typically more affordable due to the simplicity of the weave pattern and the ease of the molding process.
- 2×2 Weave:
- Strengths: Greater flexibility, able to conform to complex molds, and an attractive diagonal pattern.
- Weaknesses: Slightly less stable than the 1×1 weave due to the looser structure.
- Cost: Slightly higher due to the complexity of manufacturing and its adaptability to intricate designs.
Other Carbon Fiber Weave Patterns
While 1×1 and 2×2 weaves are the most commonly used in the automotive industry, there are several other weave patterns available, each with its own unique characteristics:
- Four-Harness Satin: Offers a smooth finish and moderate flexibility.
- Five-Harness Satin: Similar to the four-harness satin but with added drapability.
- Eight-Harness Satin: Extremely flexible, making it suitable for very complex shapes.
- 4×4 Weave: A balanced weave that offers more flexibility than 1×1 but retains strength.
- Unidirectional Weave: Reinforces strength in a single direction, often used in structural components.
- Triaxial Weave: Provides multidirectional reinforcement for enhanced strength and durability.
In summary, the choice between 1×1 and 2×2 weaves depends largely on the specific requirements of the application. For simple, flat, or gently curved parts where appearance and rigidity are priorities, the 1×1 weave is a great option. For parts with more complex shapes and angles, the 2×2 weave is the better choice due to its superior flexibility. Ultimately, both weaves provide excellent strength and lightweight properties, making them popular choices for both aesthetic and performance-driven automotive parts.
What are Epoxy, Vinylester, and Polyester Resins?
Before purchasing carbon fiber parts, it is essential to understand the resins used in their construction. This knowledge helps you gauge their effectiveness and value for the price you pay. Three primary types of resins are commonly used in automotive carbon fiber parts: epoxy, vinylester, and polyester. Understanding their properties will help you make an informed decision about which brand and type of carbon fiber parts best suit your needs.
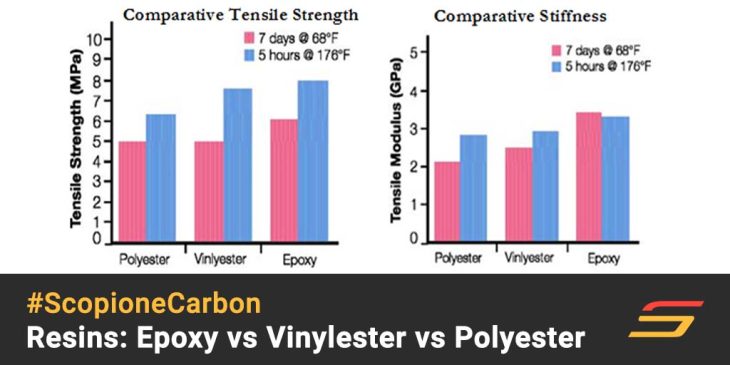
Epoxy Resin
Epoxy resin is the most expensive of the three types but also the strongest and most durable. Epoxy is a polymer resin that hardens when combined with a catalyst, forming a robust and resilient matrix. This resin binds exceptionally well to carbon fiber, Kevlar, and fiberglass, creating a solid, leak-proof barrier. Key features of epoxy resin include:
- Tensile Strength and Durability: Epoxy offers the greatest tensile strength, stiffness, and resistance to fatigue.
- Resistance to Degradation: It is highly resistant to water damage, osmosis, and chemical wear compared to polyester or vinylester resins.
Epoxy resins consist of two parts—a resin and a hardener—which must be mixed in precise proportions for maximum effectiveness. This differs from vinylester and polyester resins, which are single-component substances that only require a small amount of catalyst.
Formulations and Applications
Epoxy resins come in various formulations that cure at different temperatures and speeds. Additionally, specialized temperature-resistant epoxy compounds are available for high-performance applications. While epoxy is a superior adhesive material, it has some drawbacks:
UV Sensitivity: Epoxy can yellow when exposed to moisture and UV light. Therefore, it is crucial to choose parts with UV-protected epoxy hardeners. Brands like Scopione use epoxy resins with added UV protection to prevent discoloration and maintain the parts’ appearance and performance.
Amine Blush: A wax-like residue that forms during the curing process, which must be removed before additional layers can be applied.
Vinylester Resin
Vinylester resin is less expensive and about one-third as strong as epoxy. It does not bond as effectively to carbon fiber or Kevlar but has specific aesthetic and practical uses. Common characteristics of vinylester resin include:
- Limited Adhesion: Vinylester resin adheres better to fiberglass than to carbon fiber or Kevlar.
- Cosmetic Enhancements: Often used as a surface coating to enhance the appearance of carbon fiber parts.
Due to its moderate strength and aesthetic appeal, vinylester is primarily used for products where appearance is prioritized over structural integrity.
Polyester Resin
Polyester resin is the least expensive option and bonds poorly with carbon fiber and Kevlar. It is primarily compatible with fiberglass. Key points about polyester resin include:
- Low Bonding Strength: Polyester resin offers weak adhesion to carbon fiber and Kevlar.
- Cost-Effectiveness: While inexpensive, it is unsuitable for applications requiring high strength or durability.
Unless cost is the sole consideration and strength is not critical, polyester resin-based carbon fiber or Kevlar parts are generally not recommended for automotive applications.
Choosing the right resin for carbon fiber parts depends on your performance, durability, and budget requirements. Epoxy resin provides the highest strength, durability, and resistance to environmental factors but comes at a premium price. Vinylester offers aesthetic benefits but lacks the strength needed for high-performance use. Polyester resin, though affordable, is best suited for fiberglass-based applications and should be avoided for critical carbon fiber components.
By understanding the strengths and weaknesses of each resin type, you can make an informed decision and invest in carbon fiber parts that meet your vehicle’s needs and your performance expectations.
What are Surface Treatments and Finishes?
Surface treatments and finishes for carbon fiber components are crucial in determining their aesthetic appeal, durability, and performance. Here’s an expanded overview of common finishes:
- Glossy Finish
- Appearance: High-gloss, mirror-like surface that highlights the carbon fiber weave.
- Advantages: Enhances visual appeal; often used in cosmetic applications.
- Considerations: More susceptible to showing scratches, fingerprints, and imperfections over time; best suited for areas with minimal handling.
- Matte Finish
- Appearance: Subdued, non-reflective surface with the carbon fiber weave still visible.
- Advantages: Better at concealing scratches and fingerprints; offers a unique aesthetic; preferred for components subject to frequent handling.
- Satin Finish
- Appearance: Intermediate between gloss and matte; smooth with a soft sheen.
- Advantages: Balances reflectivity and scratch resistance; provides a refined look without the high reflectivity of gloss.
- Textured Finish (Peel-Ply)
- Appearance: Rough, sandpaper-like texture.
- Advantages: Ideal for bonding applications; the texture promotes better adhesion with adhesives or additional layers.
- Forged Carbon Finish
- Appearance: Unique, marbled pattern resulting from randomly arranged carbon fiber fragments.
- Advantages: Distinctive aesthetic; often used in luxury or high-end applications to stand out from traditional carbon fiber weaves.
- Clearcoat Finish
- Appearance: Transparent coating that can be glossy or matte, enhancing the underlying carbon fiber appearance.
- Advantages: Provides UV protection; adds an extra layer of durability; enhances visual depth.
- Sanded Finish
- Appearance: Smooth, matte-like surface achieved by sanding the outer resin layer.
- Advantages: Removes surface imperfections; prepares the component for painting or additional coatings.
- Painted Finish
- Appearance: Opaque color applied over the carbon fiber, hiding the weave pattern.
- Advantages: Offers customization in color; provides additional environmental protection; commonly used in applications like sporting goods.
Selecting the appropriate surface treatment and finish depends on the intended application, desired aesthetics, and environmental exposure of the carbon fiber component.
What are Advantages of Carbon Fiber in Automotive Applications?
Carbon fiber offers numerous advantages in automotive applications, enhancing vehicle performance, efficiency, and aesthetics. Here’s an overview:
1. Weight Reduction and Fuel Efficiency
- Lightweight Nature: Carbon fiber is significantly lighter than traditional materials like steel and aluminum, contributing to overall vehicle weight reduction.
- Improved Fuel Efficiency: Lighter vehicles require less energy to operate, leading to better fuel economy and reduced emissions.
2. Enhanced Strength and Durability
- High Strength-to-Weight Ratio: Despite its lightness, carbon fiber exhibits exceptional tensile strength, providing robust structural integrity.
- Corrosion Resistance: Unlike metals, carbon fiber does not rust or corrode, ensuring longevity and reducing maintenance costs.
3. Superior Performance and Handling
- Improved Acceleration and Braking: Reduced weight enhances acceleration and braking responsiveness, contributing to overall vehicle performance.
- Enhanced Maneuverability: Lower mass improves handling and agility, offering a more dynamic driving experience.
4. Design Flexibility and Aesthetics
- Complex Geometries: Carbon fiber can be molded into intricate shapes, allowing for innovative and aerodynamic designs.
- Distinctive Appearance: The unique weave patterns and finishes of carbon fiber add a premium, high-performance aesthetic to vehicles.
5. Thermal Stability and Safety
- High Thermal Resistance: Carbon fiber maintains structural integrity under extreme temperatures, beneficial for components exposed to high heat.
- Crashworthiness: In the event of a collision, carbon fiber can absorb and dissipate energy effectively, enhancing occupant safety.
6. Environmental Benefits
- Reduced Emissions: Improved fuel efficiency leads to lower greenhouse gas emissions, contributing to environmental sustainability.
- Recyclability: Advances in recycling technologies are making it possible to reuse carbon fiber materials, promoting a more sustainable lifecycle.
Incorporating carbon fiber into automotive design not only elevates vehicle performance and efficiency but also aligns with modern demands for sustainability and innovation.
Other Terms Explained
- What is Tow, Roving, or Strand?
- What is a Composite Material?
- What is a Matrix in Composite Materials?
- What is PAN?
- What is Filament?
- What is a Ply?
- What is Laminate?
- What is Fiber Orientation?
- How Precursors for Polyacrylonitrile (PAN) Is Created?
- What is Axial?
- What is the Autoclave Process?
- What is Carbonization?
- What is Modulus?
- What is Electrical Conductivity?
- What is Oxidation or Stabilization?
- What is Precursor?
- What is Tensile Strength?
- What is Shear Strength?
- What is Void Content?
- What is Wet Layup?
- What is Prepreg?
- What is Cure Cycle?
- What is Resin?
- What is Thermoset vs. Thermoplastic?
- What is Layup Schedule?
- What is Cross-Ply?
- What is Fatigue Resistance?
- What is Delamination?
- What is Isotropic vs. Anisotropic?
What is Tow, Roving, or Strand?
Tow is a large group of carbon fiber filaments that are bundled and packaged together onto a single spool, also known as a bobbin. Other terms for “tow” include “strand” or “roving.” The term “small tow” refers to carbon fiber rovings containing fewer than 24,000 filaments. In contrast, “large tow” refers to rovings that typically contain between 48,000 and 320,000 filaments, or sometimes even more. For example, if you see the designation “3K,” it means that the tow contains 3,000 fibers. The purpose of the tow is to provide additional strength and reinforcement to a composite structure, particularly when the fibers are aligned in specific directions to optimize their mechanical properties.
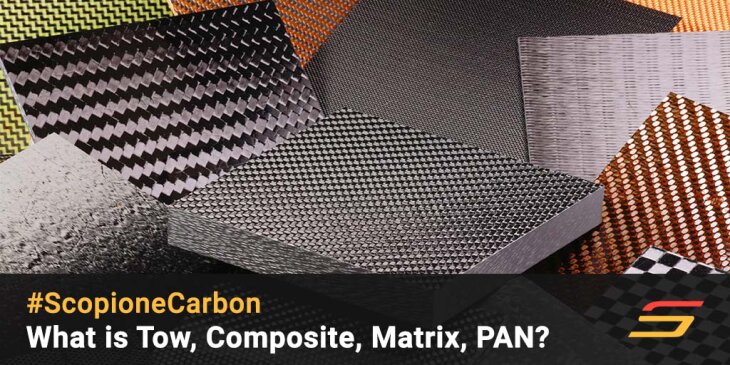
What is a Composite Material?
A composite material is formed by combining two or more distinct materials to create a final product that benefits from the strengths of each component. In carbon fiber-reinforced plastics or fiberglass, for instance, the high strength and stiffness of the carbon fibers are paired with a lightweight, stable matrix to create a material with desirable mechanical properties. For example, carbon fiber-reinforced plastics consist of carbon fibers embedded within a polymer matrix, resulting in a strong, lightweight, and durable material used in industries such as aerospace, automotive, and sporting goods.
What is a Matrix in Composite Materials?
In a composite material, the matrix is the material that surrounds and holds the reinforcing fibers in place. The matrix is typically much weaker than the fibers, especially in tension, but plays a crucial role in transferring mechanical loads between the fibers. The matrix also helps protect the fibers from environmental damage, such as moisture or impact, which can degrade performance.
What is PAN?
PAN stands for polyacrylonitrile. It is the raw material used to produce the most common type of carbon fibers. PAN-based carbon fibers are known for their exceptional tensile strength and are particularly well-suited for structural applications. They also exhibit relatively high compressive strength compared to pitch-based carbon fibers, making them ideal for applications that require both tensile and compressive resistance.
What is Filament?
A filament is a single, continuous strand of material, typically very fine in diameter. In carbon fiber manufacturing, multiple filaments are bundled together to form a “tow.” These individual filaments contribute to the overall tensile strength and stiffness of the composite material.
What is a Ply?
A ply refers to a single layer of fiber-reinforced material, such as carbon fiber or fiberglass. In composite construction, multiple plies are layered in different orientations to optimize strength and stiffness in multiple directions.
What is Laminate?
A laminate is a structure made by stacking multiple plies or layers of composite material. The performance of a laminate depends on the type of fibers, the matrix material, and the orientation of each ply.
What is Fiber Orientation?
Fiber orientation describes the direction in which the fibers are aligned within a composite ply. Common orientations include 0°, 45°, and 90° angles. Proper fiber orientation is critical for ensuring the composite can withstand forces in specific directions.
How Precursors For Carbon Fiber Polyacrylonitrile (PAN) Is Created?
What is Axial?
Axial refers to a characteristic or property aligned with the direction of the fiber orientation. In the context of composite materials, “axial” typically describes forces or stresses applied parallel to the fiber direction, where the fibers exhibit maximum strength and stiffness.
What is the Autoclave Process?
The autoclave process involves placing an object inside a sealed vessel where it is subjected to controlled levels of heat and fluid pressure. This process is commonly used in the production of high-performance composite materials, such as carbon fiber components, to ensure thorough bonding and curing of the materials.
What is Carbonization?
Carbonization is the thermal process in which stabilized PAN fibers or pitch fibers are heated to temperatures between 1200°C and 1500°C. During this process, non-carbon elements are driven off, leaving behind fibers composed almost entirely of carbon. This transformation maximizes the strength of the fibers and enhances their modulus (stiffness).
What is Modulus?
Modulus is a measure of a material’s stiffness, defined as the ratio of stress to strain within the elastic range of the material. A higher modulus indicates a stiffer material, which resists deformation under applied loads. Carbon fiber is prized for its high modulus, which makes it ideal for applications that require minimal deflection or bending.
What is Electrical Conductivity?
Electrical conductivity measures a material’s ability to conduct electrical current. Carbon fiber, for example, is an excellent conductor of electricity, while fiberglass is not. In boat construction, electrical conductivity is an important consideration due to the risk of galvanic corrosion, which can occur when dissimilar conductive materials are exposed to an electrolyte, such as seawater.
What is Oxidation or Stabilization?
Oxidation or stabilization is a thermal process where the PAN precursor undergoes chemical changes that transform it into a cross-linked, thermoset material. This stabilized material can maintain its structural shape during the subsequent carbonization process, making it a crucial step in the production of carbon fibers.
What is Precursor?
A precursor is the raw material used to create carbon fibers. For PAN-based carbon fibers, the precursor is polyacrylonitrile. For pitch-based carbon fibers, the precursor materials are derived from petroleum-based or coal tar-based compounds. The choice of precursor significantly influences the properties of the resulting carbon fibers, such as strength, stiffness, and cost.
What is Tensile Strength?
Tensile strength is the maximum amount of tensile (pulling) stress that a material can withstand before breaking. Carbon fiber is known for its exceptionally high tensile strength, making it ideal for applications where tension forces are prevalent.
What is Shear Strength?
Shear strength refers to a material’s ability to resist sliding forces along a plane. In composite materials, shear strength is an important property, particularly at the interface between fibers and the matrix.
What is Void Content?
Void content refers to the amount of air pockets or voids present within a composite material. High void content weakens the composite and reduces its mechanical properties. Proper processing methods, such as using an autoclave, minimize void content and improve overall strength.
What is Wet Layup?
Wet layup is a method of composite fabrication where fiber materials (such as carbon fiber sheets) are manually laid out and impregnated with liquid resin before being cured. It is a more labor-intensive and lower-cost process compared to automated methods like prepreg layup.
What is Prepreg?
Prepreg refers to fiber reinforcements (such as carbon fiber fabric) that have been pre-impregnated with a specific amount of resin and partially cured. Prepregs offer precise control over the resin-to-fiber ratio and are commonly used in high-performance applications such as aerospace and motorsports.
What is Cure Cycle?
A cure cycle is the specific sequence of temperatures, pressures, and times used to cure a composite material. Proper curing is essential to achieve optimal bonding and mechanical properties of the composite.
What is Resin?
Resin is the polymer material that forms the matrix in composite materials. Common types of resins used in composites include epoxy, polyester, and vinyl ester. The resin binds the fibers together and provides shape, durability, and resistance to environmental conditions.
What is Thermoset vs. Thermoplastic?
- Thermoset resins, such as epoxy, undergo an irreversible chemical reaction during curing, creating a rigid structure.
- Thermoplastics can be heated, reshaped, and cooled multiple times, making them more versatile but often less stiff compared to thermosets.
What is Layup Schedule?
A layup schedule is a detailed plan that specifies the number, type, and orientation of the plies in a laminate. It ensures that the composite is manufactured to meet specific performance criteria.
What is Cross-Ply?
Cross-ply refers to a laminate design where layers are alternately oriented at 0° and 90° angles. This configuration provides balanced strength and stiffness in perpendicular directions.
What is Fatigue Resistance?
Fatigue resistance is a material’s ability to withstand repeated cycles of loading and unloading without failure. Carbon fiber composites generally have excellent fatigue resistance, making them ideal for applications subjected to cyclic stresses, such as wind turbines and aircraft structures.
What is Delamination?
Delamination occurs when layers within a laminate separate or peel apart, usually due to defects, impact damage, or improper bonding. Delamination can significantly weaken the structure and reduce its mechanical performance.
What is Isotropic vs. Anisotropic?
- Isotropic materials have uniform mechanical properties in all directions.
- Anisotropic materials, such as carbon fiber composites, have different properties depending on the direction of the applied load. This makes fiber orientation crucial in composite design.
Frequently Asked Questions (FAQs)
Why is carbon fiber used in automotive parts?
- Answer: Carbon fiber is a lightweight, high-strength material composed of thin strands of carbon atoms. These strands are woven into fabrics and combined with resins to create composite materials. In automotive applications, carbon fiber is favored for its superior strength-to-weight ratio, enhancing vehicle performance, fuel efficiency, and aesthetics.
How does carbon fiber compare to traditional materials like steel or aluminum?
- Answer: Carbon fiber offers comparable or superior strength to steel and aluminum but at a fraction of the weight. This weight reduction leads to improved acceleration, handling, and fuel efficiency in vehicles. Additionally, carbon fiber is corrosion-resistant and can be molded into complex shapes, providing both functional and aesthetic benefits.
What are the differences between dry (pre-preg) and wet carbon fiber?
- Answer: Dry carbon fiber, or pre-preg, involves fibers pre-impregnated with resin, allowing for precise resin control and resulting in higher strength and lighter weight. Wet carbon fiber is manually coated with resin during the molding process, which can lead to variations in resin content and potentially lower strength-to-weight ratios.
Can carbon fiber parts be repaired if damaged?
- Answer: Yes, carbon fiber parts can often be repaired, depending on the extent and location of the damage. Minor surface scratches can be polished out, while more significant structural damage may require professional assessment and repair to ensure safety and integrity.
How should I care for and maintain carbon fiber components on my vehicle?
- Answer: To maintain carbon fiber parts, regularly clean them with a soft cloth and mild soap. Avoid abrasive cleaners or tools that could scratch the surface. Applying a UV-protectant can help prevent sun damage, and promptly addressing any chips or cracks will maintain both appearance and structural integrity.
Are carbon fiber parts compatible with all vehicle models?
- Answer: Compatibility depends on the specific part and vehicle model. It’s essential to verify that the carbon fiber component is designed for your vehicle’s make and model to ensure proper fitment and functionality. Consulting with the manufacturer or a knowledgeable retailer can provide guidance on compatibility.
Do carbon fiber parts affect vehicle safety?
- Answer: High-quality carbon fiber parts are designed to meet or exceed safety standards. However, it’s crucial to ensure that any aftermarket parts are properly installed and compatible with your vehicle. Improper installation or the use of substandard components can negatively impact safety.
Why do some carbon fiber parts have different weave patterns, and do they affect performance?
- Answer: Different weave patterns, such as plain weave or twill weave, primarily affect the aesthetic appearance of carbon fiber parts. While the weave can influence the material’s flexibility and drapability during manufacturing, it generally does not significantly impact the performance of the finished component.
Are there color options available for carbon fiber parts?
- Answer: Traditional carbon fiber has a distinctive black or dark gray appearance due to its natural composition. However, colored carbon fiber can be produced by incorporating pigments into the resin or using colored fibers, allowing for customization to match personal preferences or vehicle aesthetics.
Is carbon fiber resistant to corrosion?
- Answer: Yes, carbon fiber is naturally resistant to corrosion, unlike metals that can rust over time. This property makes it particularly advantageous for automotive parts exposed to various environmental conditions, ensuring longevity and reduced maintenance.
Is carbon fiber environmentally friendly?
- Answer: The production of carbon fiber involves energy-intensive processes, raising environmental concerns. However, the use of carbon fiber in vehicles can lead to weight reduction, improving fuel efficiency and reducing emissions over the vehicle’s lifespan. Additionally, advancements in recycling technologies are being developed to address end-of-life disposal of carbon fiber components.
Care and Maintenance of Carbon Fiber Parts
Proper care and maintenance of carbon fiber automotive parts are essential to preserve their appearance, structural integrity, and longevity. Here’s an expanded guide to help you maintain your carbon fiber components effectively:
1. Regular Cleaning
- Gentle Washing: Use a mild automotive-specific cleaner or pH-neutral soap with a soft microfiber cloth to clean carbon fiber surfaces. Avoid harsh chemicals, as they can damage the clear coat protecting the carbon fiber.
- Avoid Abrasive Materials: Steer clear of abrasive brushes or rough sponges that could scratch the surface. Instead, opt for soft-bristled brushes or microfiber towels to gently remove dirt and grime.
2. Protection from UV Exposure
- UV-Resistant Coatings: Apply a high-quality wax or ceramic coating that offers UV protection to shield the carbon fiber from sun damage. Regular application helps maintain the glossy finish and prevents oxidation.
- Parking Considerations: Whenever possible, park your vehicle in shaded areas or use a car cover to minimize direct sunlight exposure, reducing the risk of UV-induced fading or discoloration.
3. Inspection and Damage Prevention
- Regular Inspections: Periodically examine carbon fiber parts for signs of damage, such as cracks, chips, or delamination. Early detection allows for timely repairs, preventing further deterioration.
- Avoid Chemical Exposure: Keep carbon fiber components away from harsh chemicals like gasoline, brake fluid, or solvents, as they can corrode or damage the surface. In case of accidental exposure, clean the area immediately with a mild soap and water solution.
4. Polishing and Restoration
- Addressing Oxidation: If the carbon fiber surface becomes oxidized or yellowed, use a fine-grade polish with a soft polishing pad to restore clarity and shine. For heavily oxidized surfaces, professional restoration may be necessary.
- Protective Coatings: After polishing, apply a protective sealant or ceramic coating to enhance the surface’s resistance to environmental factors and maintain its luster.
5. Maintenance Best Practices
- Avoid High-Pressure Washing: Refrain from using high-pressure water jets directly on carbon fiber parts, as they can cause delamination or force water into areas that may lead to damage. Instead, use a gentle stream of water during cleaning.
- Temperature Considerations: Protect carbon fiber components from extreme temperatures, as excessive heat can affect the resin matrix, leading to potential structural issues. Avoid parking near heat sources or exposing the vehicle to extreme cold without adequate protection.
By following these guidelines, you can ensure that your carbon fiber automotive parts remain in excellent condition, enhancing both the aesthetic appeal and performance of your vehicle.
Congratulations! You now have a comprehensive understanding of the fundamental terminology associated with the carbon fiber parts production process. At Scopione, we are dedicated to delivering the highest quality carbon fiber components and providing exceptional customer service. Our team of experts is always available to answer any questions you may have—whether they pertain to the terminology explained on this page or any other aspect of carbon fiber parts.
We believe that education and open communication are key to ensuring our customers receive the best possible products and service. By equipping our customers with essential knowledge, we aim to create a seamless and rewarding experience that fosters confidence and trust.
In addition to offering premium carbon fiber parts, we provide a wide range of customization options. We understand that each customer has unique preferences and requirements, which is why we are committed to offering tailored solutions that meet your specific needs. Whether you are looking for unique finishes, custom dimensions, or specialized performance attributes, our customization process is designed to bring your vision to life.
Furthermore, at Scopione, we continuously invest in research and development to stay at the forefront of the carbon fiber industry. Our team is dedicated to exploring and testing new materials, designs, and manufacturing techniques to ensure our products remain cutting-edge and of superior quality. This commitment to innovation allows us to offer durable, lightweight, and high-performance components that exceed industry standards.
To summarize, Scopione is dedicated to providing industry-leading carbon fiber parts backed by exceptional customer support, versatile customization options, and a strong commitment to research and innovation. We encourage you to reach out with any questions or requests—our team is ready to assist you at every step of the way. Thank you for choosing Scopione; we look forward to serving you with unparalleled products and service.
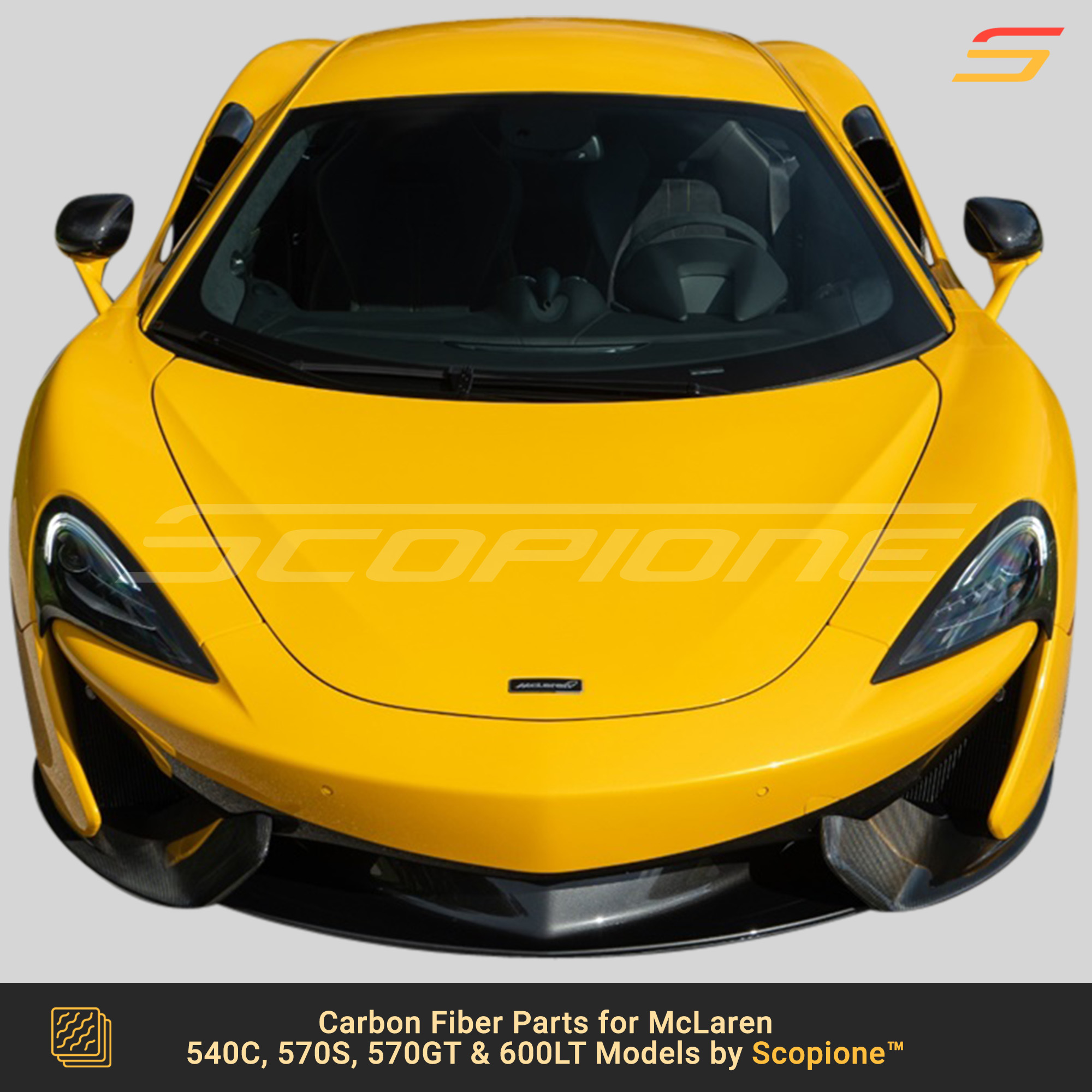
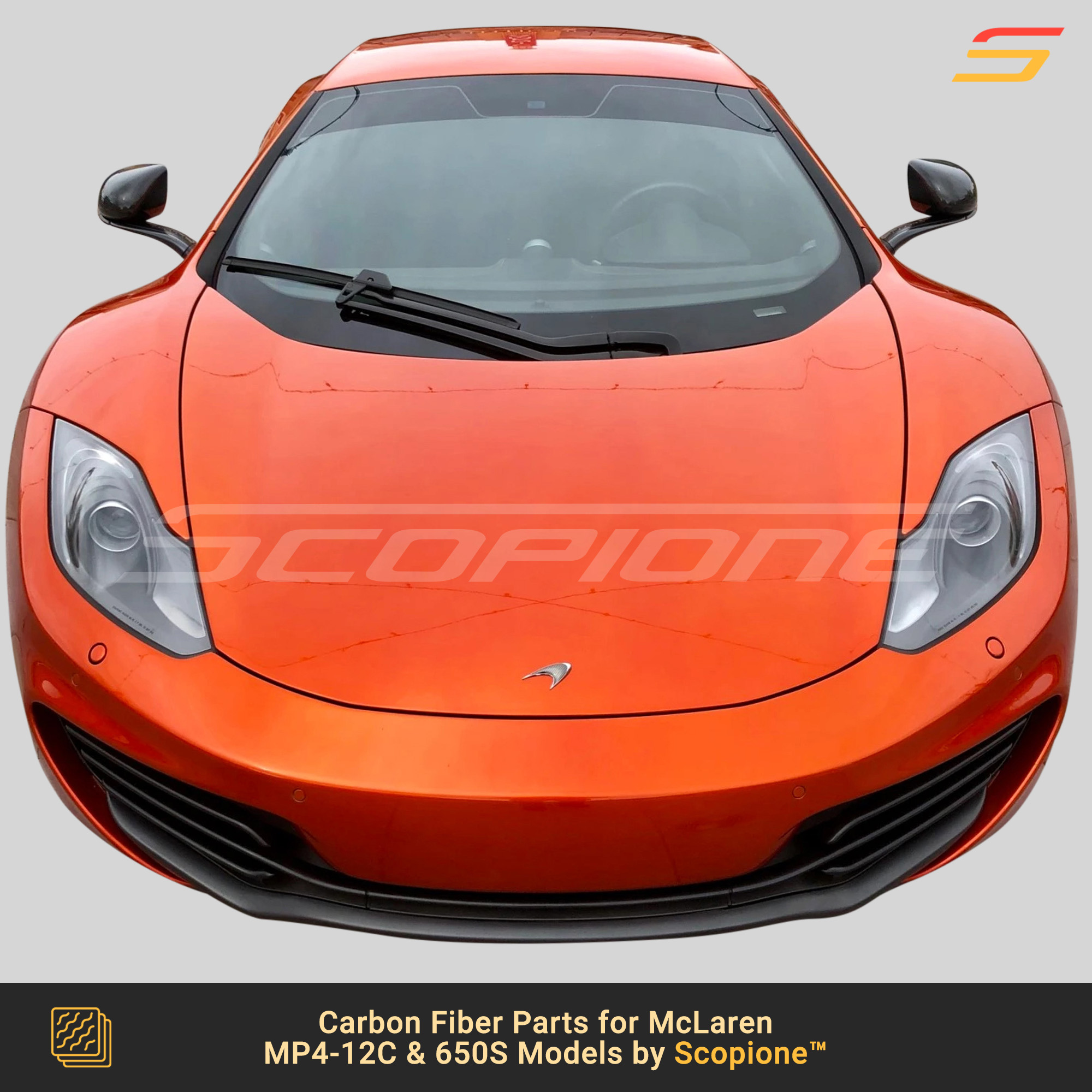
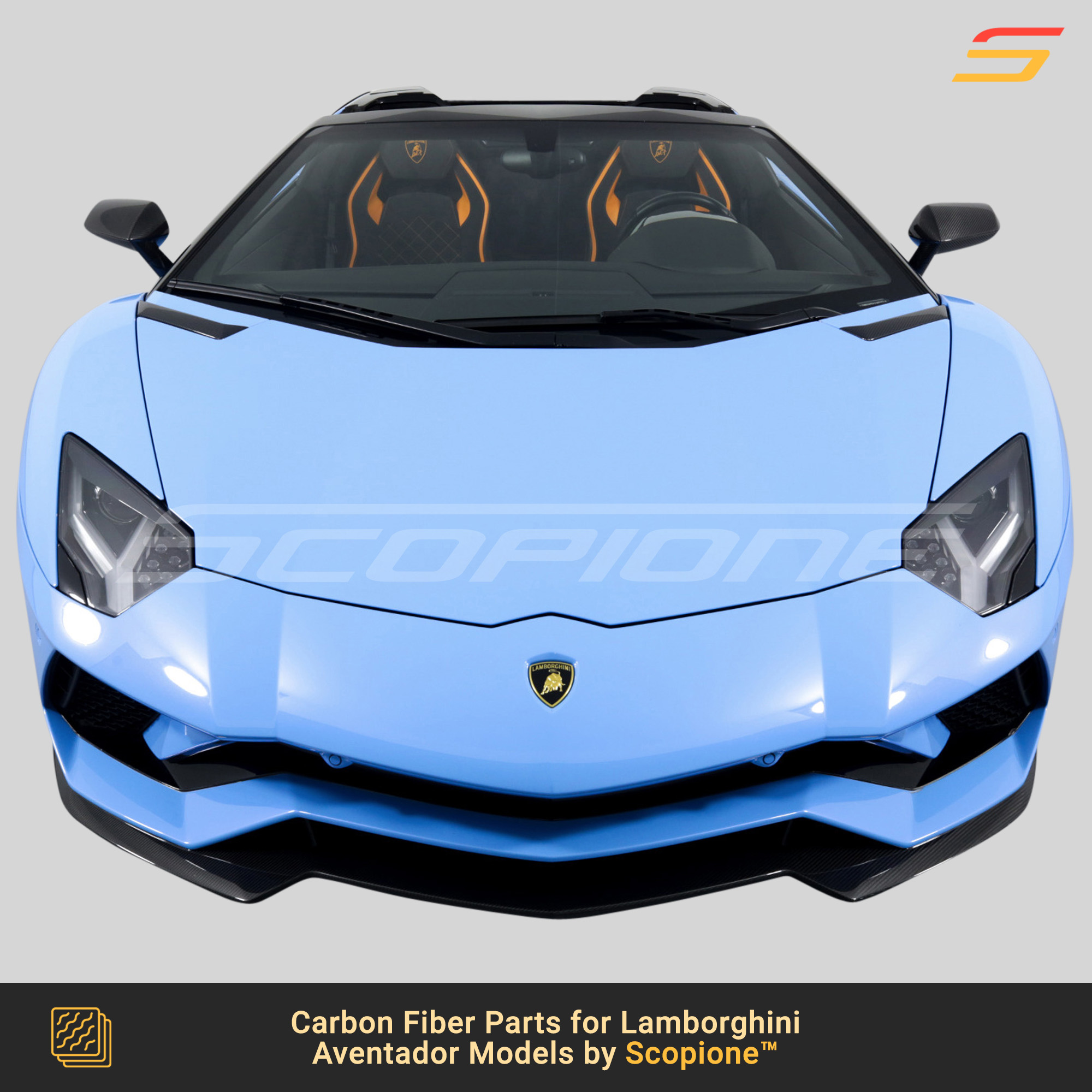
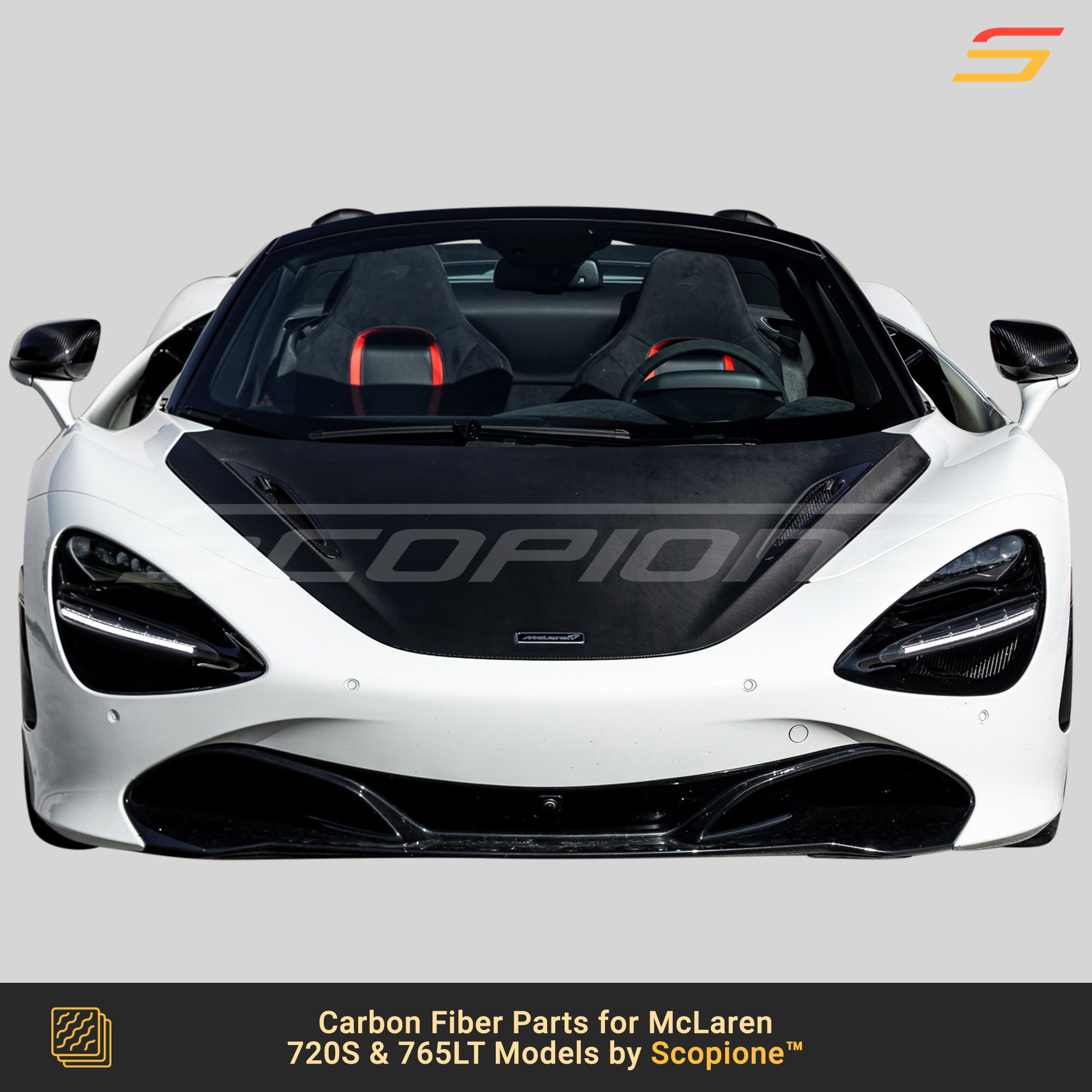
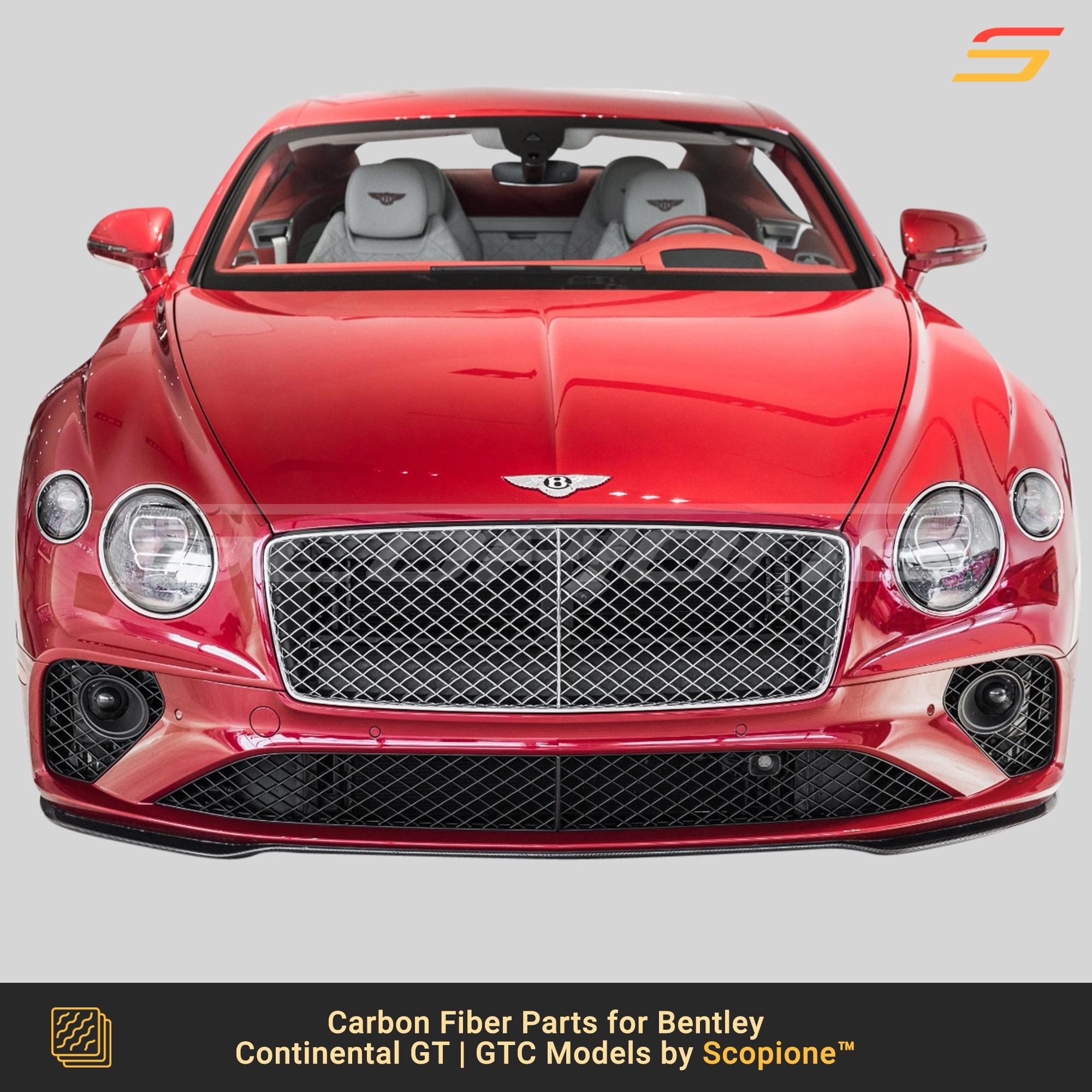
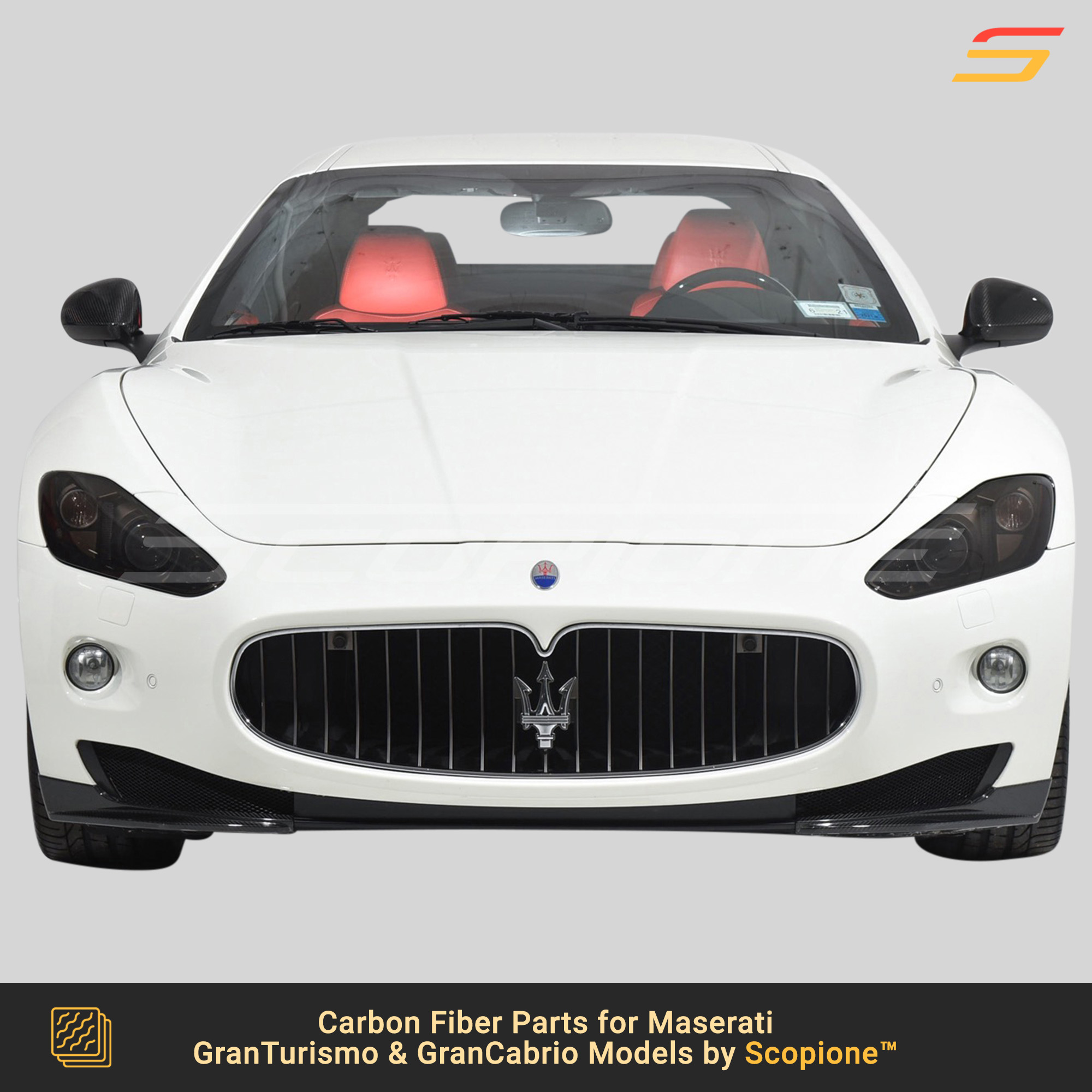
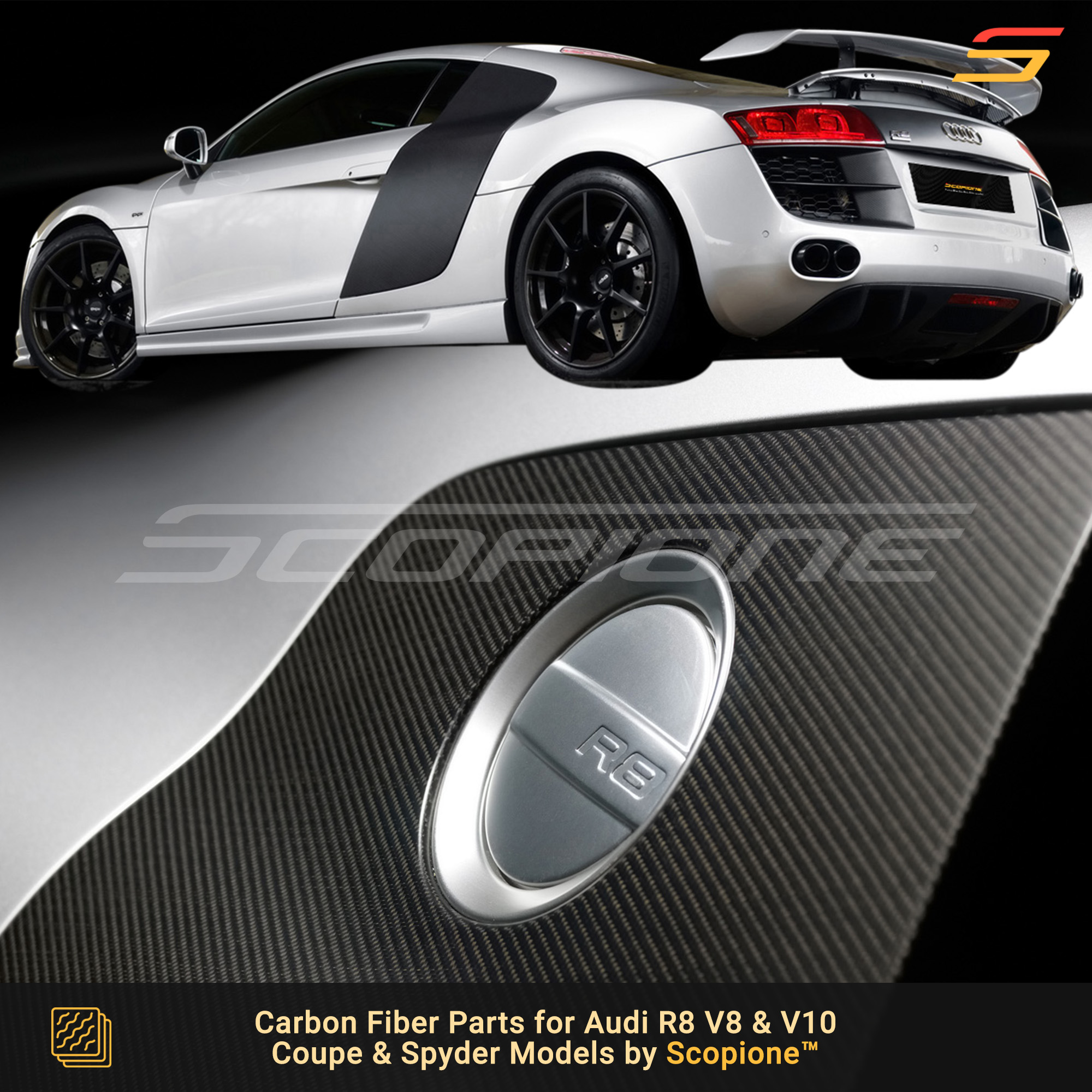
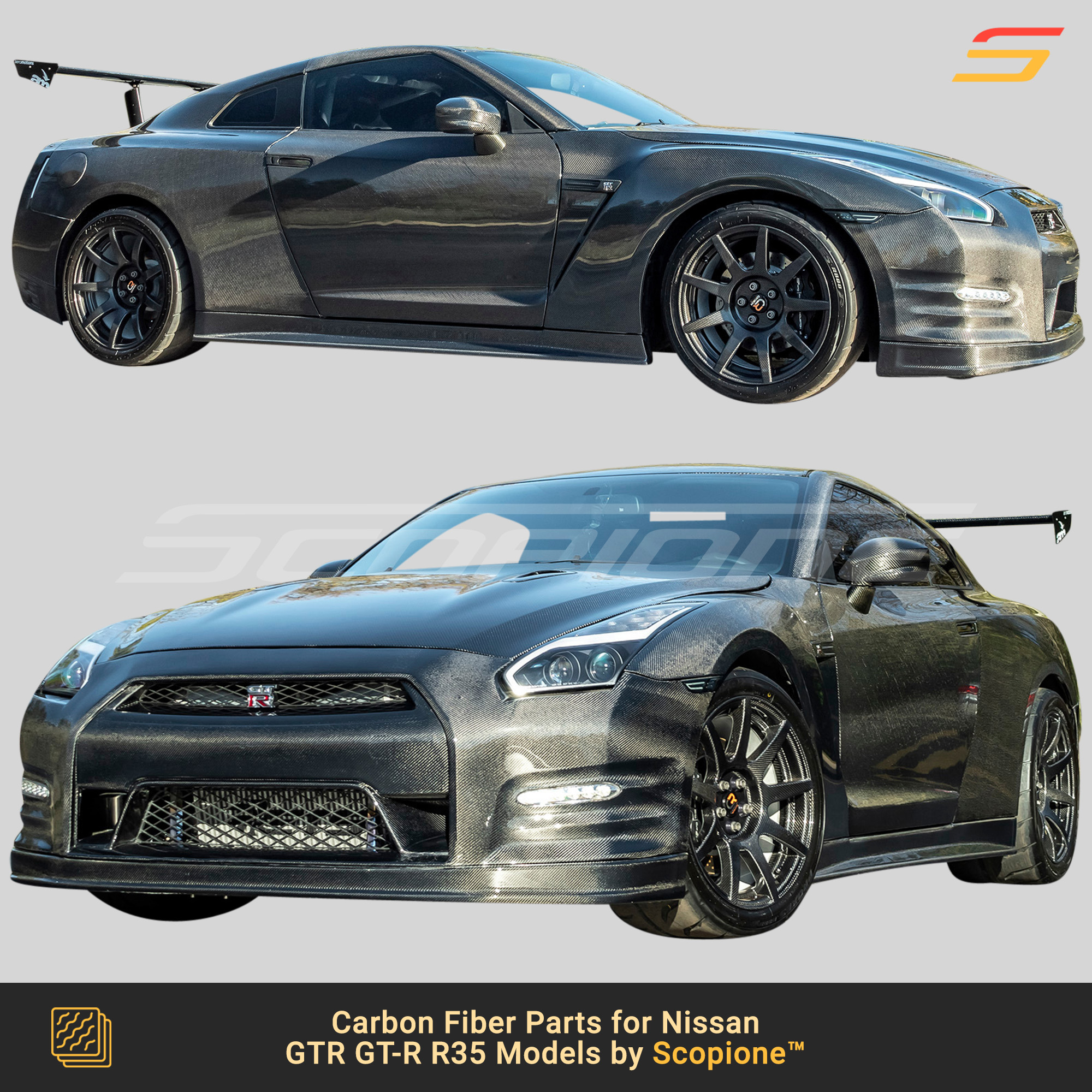
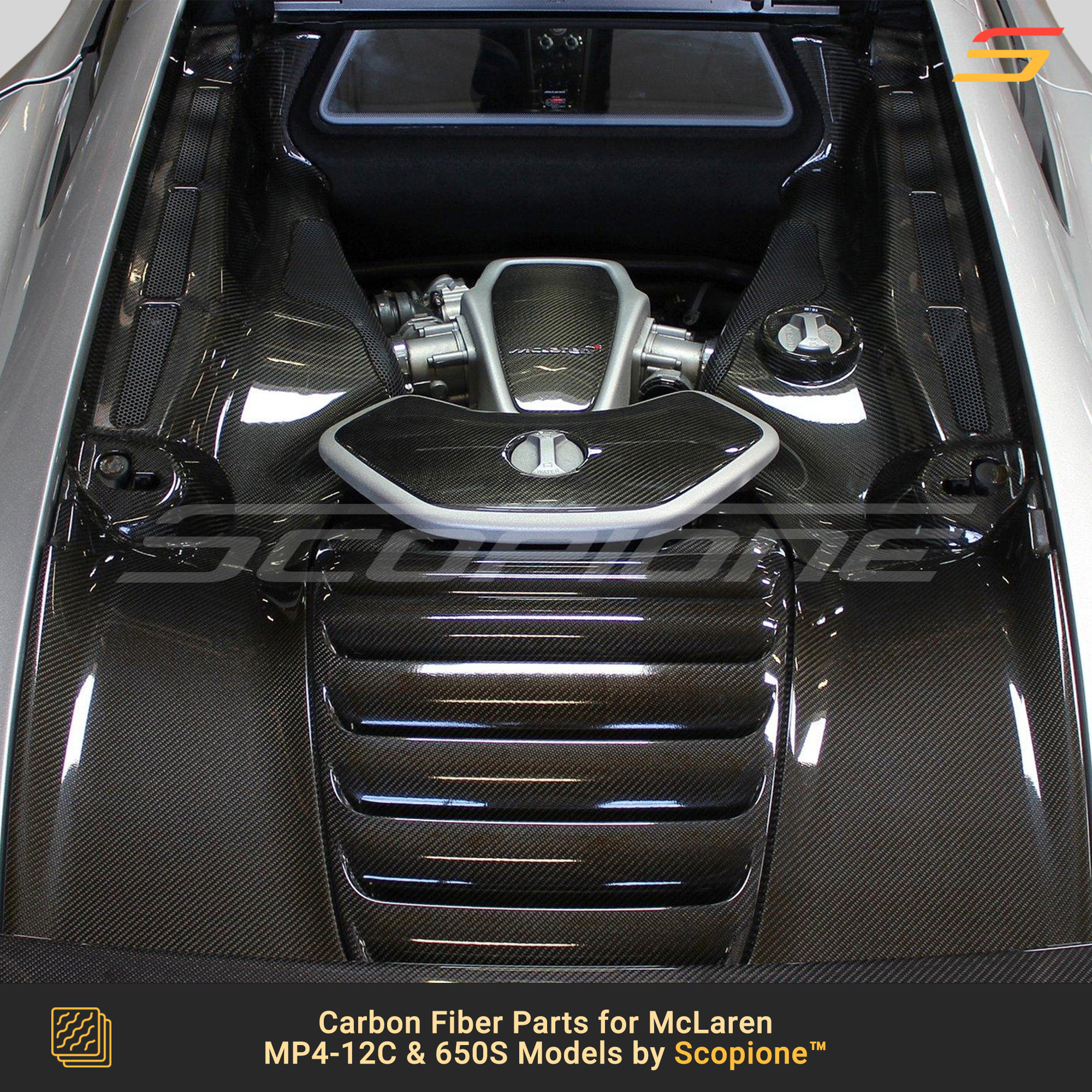
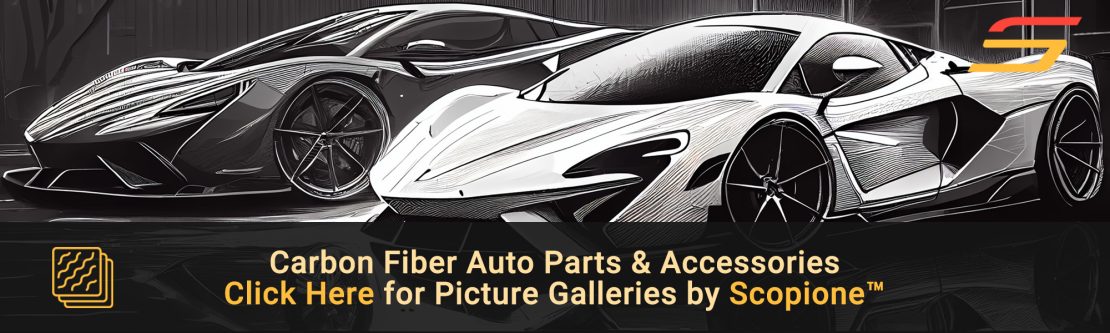